Home : Technical : Detachable
Lifts : Terminals/Stations : Cadence
Systems
Cadence Systems: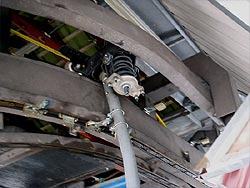
By: John Holm & Ryan B
Some terms:
Passive cadencing: More commonly known as the chain
system, this consists of a chain with a specifically spaced set
of teeth on one end of the lift, and a conveyor with teeth on every
link on the other end. Both chains run at a constant speed. The
cadence chain captures the chair, carries it around the contour,
and puts it into the acceleration tyre bank for the trip up (or
down) the hill. The conveyor chain does the same, except it does
not space the chair. The speed of both chains can be varied to suit
several conditions: the conveyor can be sped up or slowed down depending
upon temperature, and the cadence can be adjusted for different
chair spacing. Both should match as closely as possible, else chair
spacing gets out of sync. More on this in a bit.
Active cadencing: The current standard, this is
where there are one or two clutches attached to parts of the tyre
bank which can very the speed of that set of tyres. The PLC uses
the zone switches inside the terminal to turn the clutch(es) on
or off depending upon the space of the chair.
Problems with both types:
Chain systems are highly susceptible to temperature. For example, on a very
cold day, the haul rope shrinks, bringing the carriage forward.
Because of this, the position of the rope in relation to the chain
changes (in this case, the rope literally moves further from the
chain) causing the chairs to 'come in late'. The opposite occurs
on a warm day. The problem can be solved by speeding up or slowing
down the conveyor on the opposite end of the lift; if you speed
it up you overcome the late issue by placing the chairs 'ahead'
on the rope. Of course, when it warms up the chairs then stall out
at the end of the tyre bank while waiting for the teeth, so you
then have to slow the conveyor chain down.
Active systems eliminate the problems associated with chains, but
have a few of their own. In a chain system, if a chair is out of
whack it is easy to respace (simply move the chair forward or backward
into the teeth). In an active tyre system, it may take several laps
to respace as the clutch can only advance or retard a carrier by
a few feet at one time. If the clutch goes out (usually an electrical
problem) there is no spacing going on at all and it is nearly impossible
to fix this.
Zones and anticollision faults: The lifts PLC
monitors the spacing of carriers in the terminals by a system of
sensors located at intervals around the rail. Each zone has a time
value associated with it; if a carrier is in the zone longer than
that value the lift will shut down. This prevents phisical collisions
between chairs. If a chair were to stall at the end of the tyre
bank, it would cause a zone fault. This is why one needs to monitor
where the chairs are arriving in relation to the chain teeth, on
that type of system.
I hope this answers some questions. Feel free to post any others
in the forum that you may you may have.
- John Holm
Older style Gondolas with human conveying systems used steeper
sloped deceleration/acceleration tracks (gravity never sleeps) as
a design element. The sloped tracks were set to work best in the
upper speed ranges. Of course there were a few tiny things the operator
had to be aware of.
At slow speeds the carrier never quite made
it up the deceleration ramp, this required a push from the operator
or the car rolled back to the haulrope detaching area.
At full speed
with a full load the car had enough momentum to make the 180 degree
turn after detaching, which was ok unless there was a car in the
turn.
The anti-collision system was an operator who stood between
the cabins and pushed or pulled as necessary, they also doubled
as the power for "conveying" the carrier to the launch area. The
spacing system was an operator who adjusted cabins by referencing
"match marks" painted on the track for proper distance.
The acceleration
area track sloped down to help assist the launching operator push
the carrier toward the up-line haul rope. Carrier spacing for attachment
was more of an art than science… push sorta hard after the loaded
car passes the bent I-beam unless we're on slow speed then wait
until it passes the red angle iron.
Needless to say, if grip speed
and rope speed often didn't match this would impart a large jerk
to the carrier, which caused grip wear, which helped to employ lift
mechanics.
- Ryan B |